Just 'Cuz Robotics
Hybrid Hubmotor RDY-5735: Battle Ready with Flexibility
Hybrid Hubmotor RDY-5735: Battle Ready with Flexibility
Share
Couldn't load pickup availability
The Ultimate Hybrid Hubmotor for Midcutters, Undercutters, and More!
After pioneering the world's first off-the-shelf hubmotor, we've taken everything we learned and created something new!
- 49 grams lighter than RDY-5536 with blade hardware
- Through shaft shoulder bolt
- Center or offset blade mounting
- Epoxy battle-hardened magnets and 2812 stator
- All at a lower price!
The RDY-5735 is the world's first hybrid hubmotor for beetleweight combat robots! This means it can be used for undercutters or midcutters, and while optimized with low 750 and 950kV for horizontals, it will work great for larger-diameter or higher voltage vertical spinners too. Utilizing a through shaft design, you can use the included high-strength shoulder bolt to tie your bot's frame rails together structurally and support the motor. Torx is the best, so the included custom shoulder bolts use a T25 Torx drive and low-profile heads to save weight and improve repairability. Mounting the motor requires just 3x M5 bolts (not included) and an included 8mm shoulder bolt.
Update 5/25/25: after seeing feedback from our early adopters, it seems the mechanical design of this first-gen motor isn't as robust as we had hoped when supported on just one side for undercutter/overhead spinner applications. It should still work well if supported with the longer shoulder bolt on both sides. Improvements will be made in the next batch to improve functionality for undercutters!
What's Included when you buy a Complete Motor:
- 🛠️ 1X RDY-5735 Hubmotor – Combat-ready out of the box
- 🔩 4X M5 x 12mm Class 12.9 Screws – For blade mounting
- ⚙️ 2X Custom T25 Torx Low Profile Shoulder Bolts – 8mm x 45mm, and 28mm
- 🔧 1X M6 Class 10.9 Nylock Nut
- 🔌 1X MR30-M Connector (Pre-Soldered) & 1X MR30-F Connector
Yup, that's right, TWO shoulder bolts, a lock nut, and an MR30 connector pair are included!
Replacement magnet rings are expected late April/early May 2025.
Specs and Usage
Specs
- Dimensions: 57mm outer can diameter, 35mm length
- Stator Size: Roughly 28 x 12mm (Same as the RDY-5536)
-
Weight:
- 153.7 grams for Motor + Washer Only with MR30 connector and long wires
- 163g: Above + 4X M5 x 12mm blade mount screws (49g lighter than 5536!)
- 181g: Above with 28mm long shoulder bolt and M6 lock nut
- 188g: with 45mm long shoulder bolt + nut
- Bearings: Gigantic 6805 bearing on one side, and beefy 6900 on the other
- KV: 950kV or 750kV
- Voltage: 950kV 3S-6S, 750kV 4S-8S with appropriate ESCs
- No circlips, belts, or set screws!
- Super strong, curved neodymium magnets
- Epoxied magnets for extra durability
- High-temperature copper windings
- 18AWG, 18 cm (~7 inch) long silicone wires rated to 200 degrees C
- MR30 connector preinstalled on the motor
- Winding Resistance:
- 750 kV ~124 milliohms
- 950 kV ~144 milliohms
CAD download includes blades with the proper spline geometry needed. We recommend offsetting the spline by about 0.010" (0.25mm) from the actual motor profile for a better weapon blade fit.
Note: The first time this motor is spun up it may draw unusually high current even with no load. This is normal and seems to be a result of the big bearings and their grease needing to warm up and distribute evenly. After a couple of minutes the no load current for the motor drops significantly as the motor and bearings heat up. The outside of this motor is like a big heatsink and can get very hot!
Bolt Length Recommendations:
The blade mounting flange is 6mm thick, and included M5x12mm bolts will work for any blade up to 1/4" or 6mm thick. For thicker blades, we recommend longer screws to fully engage the 6mm thick flange.
WARNING: AVOID THREADING MOUNTING SCREWS IN TOO FAR! The mounting for this motor is M5 x 7mm depth threads, threading in further than this risks damaging the stator coils. Just make sure your screws are the correct length to clamp the motor to your frame, with 5mm-7mm of thread engagement.
Comparison with RDY-5536
Power and ESCs
For best results, pair with our very own Pariah 70A ESC or our brand new RevvitRC 50A AM32 ESC, as the lower KV for this motor means less current draw, and the RevvitRC has better low-end torque performance than the Pariah in our testing.
This is a custom motor and not a conventional one so a propeller chart is a useless stat to compare this to. You should use a 50A or greater rated ESC.
Actual current draw and torque are highly dependent on your exact ESC and configuration, battery, voltage, and loading. Air resistance and tip speed for your weapon play a huge role in the current draw of your system. Even reducing speed by 20% might cut air resistance in half.
Experimental Bench Test Data: (Using Pariah 70A ESC)
This product is brand new so more testing is required, but some quick preliminary data can be found here. Expect that the motor performance is very similar to the 5536 900kv for the 950kV variant of this motor.
9" x 1/4" Blade, 750kV motor:
6S 1300mAh LiPo - Peak 70.4 Amps, 1195 Watts on spinup, continuous 36-40A ~600W
4S 850mAh GNB 120C LiHV - Peak 38.4A (seems low, likely kv mismatch AM32 settings), Continuous 29A ~260W (severe voltage sag to ~12.1V, recommend a significantly larger battery)
3S 5000mAh LiPo - Peak 30.1A (seems low, likely kv mismatch AM32 settings), Continuous 23A ~220W
Disclaimer
Warning: combat robots are not toys! They are extremely dangerous. Click here for a safety video.
Testing a robot with an active spinning weapon should never be done while maintaining a line of sight with the robot. Ideally, you should be testing inside an enclosed box or arena with at least 1/4" thick polycarbonate windows or top to see through, and 1/2” or thicker plywood or MDF construction. Operation (Including testing) outside of a suitable arena or test box could cause serious injury. By purchasing this product you acknowledge that you are responsible for the safe use of this product and that Team Just ‘Cuz Robotics or its employees are not liable for any injuries or damages.
I wanted to leave a review that may be more specific to my use case, but was very positive none the less. I paired these with an 80A ESC on Murphy's Law at June NHRL with great success. The motors themselves had plenty of power with a 6.5" diameter 1/4" blade, however, my design is probably a prime candidate to avoid some of the issues that Seth has acknowledged and is currently working on. Having forks and a giant wedge to lead into weapons allowed the motor to do exactly what I needed which was chip away at tires and armor. Overall, I will continue running these in my bot based on my use, and would recommend you consider how these will be used when purchasing. Overall I was VERY pleased with my purchase, and cant wait to run V2 when released.
Well they are motors. They broke but can modify to be a bit better by loctiteing the bearing in and also make sure you put the lock nut in the motor and not in the frame of your robot a tight grip for the shoulder bolt is a must for this motor you also will need a big esc to run them
With a big weapon blade. Overall if you absorb need a hubmotor for an undercuter they are fine but would not absolutely recommend until there is a revision that fixes the bottom bearing.
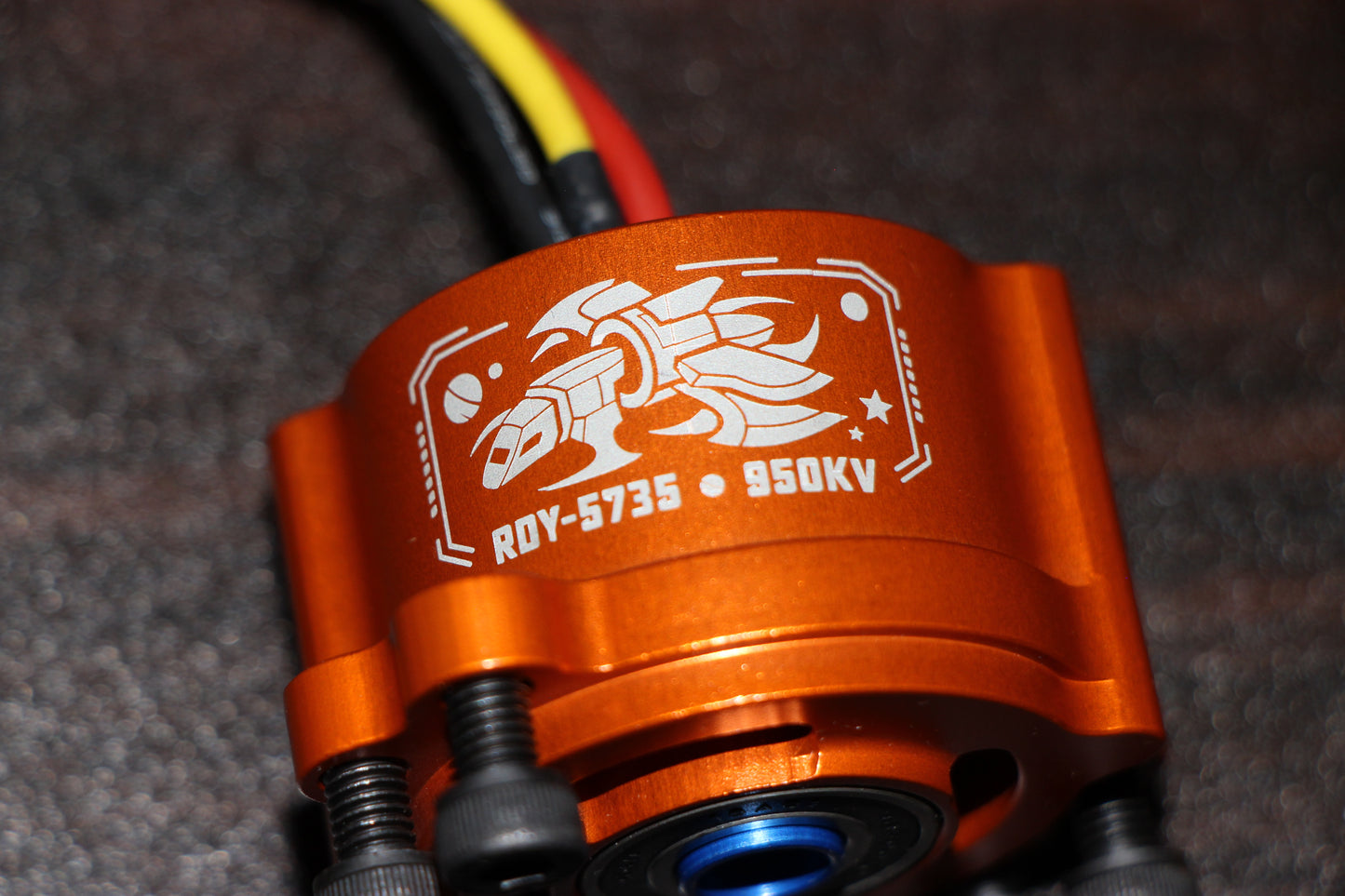


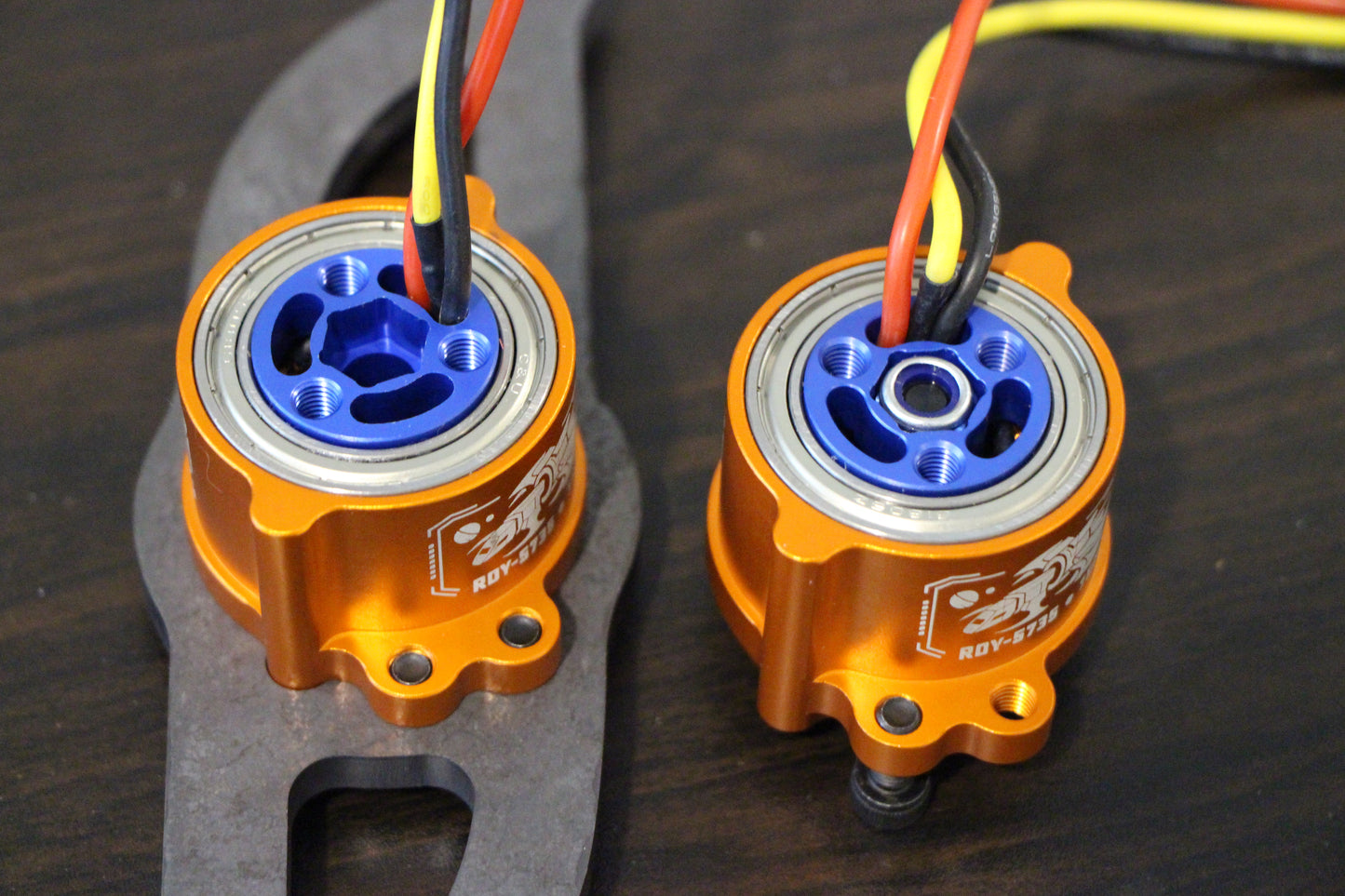
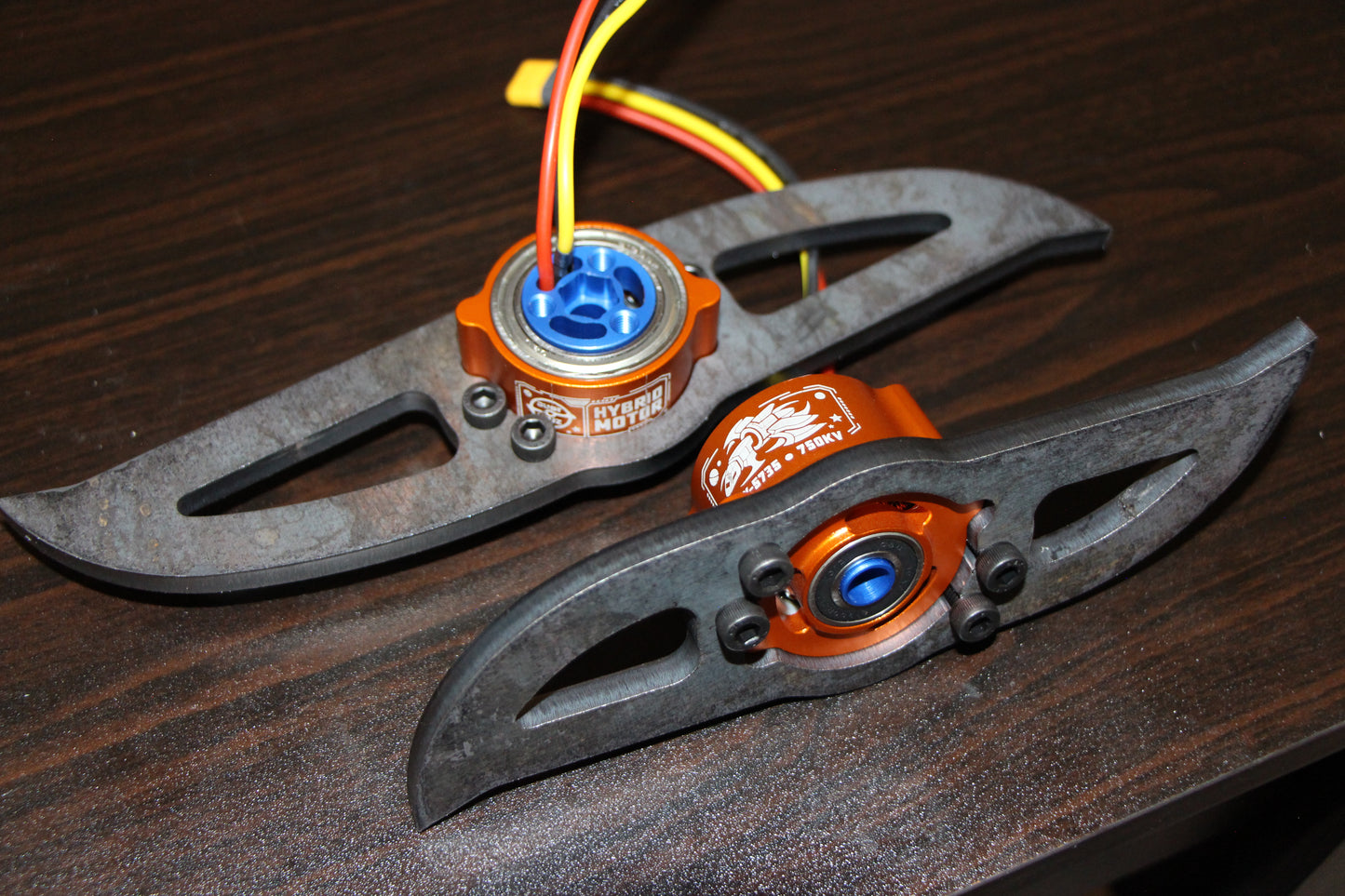
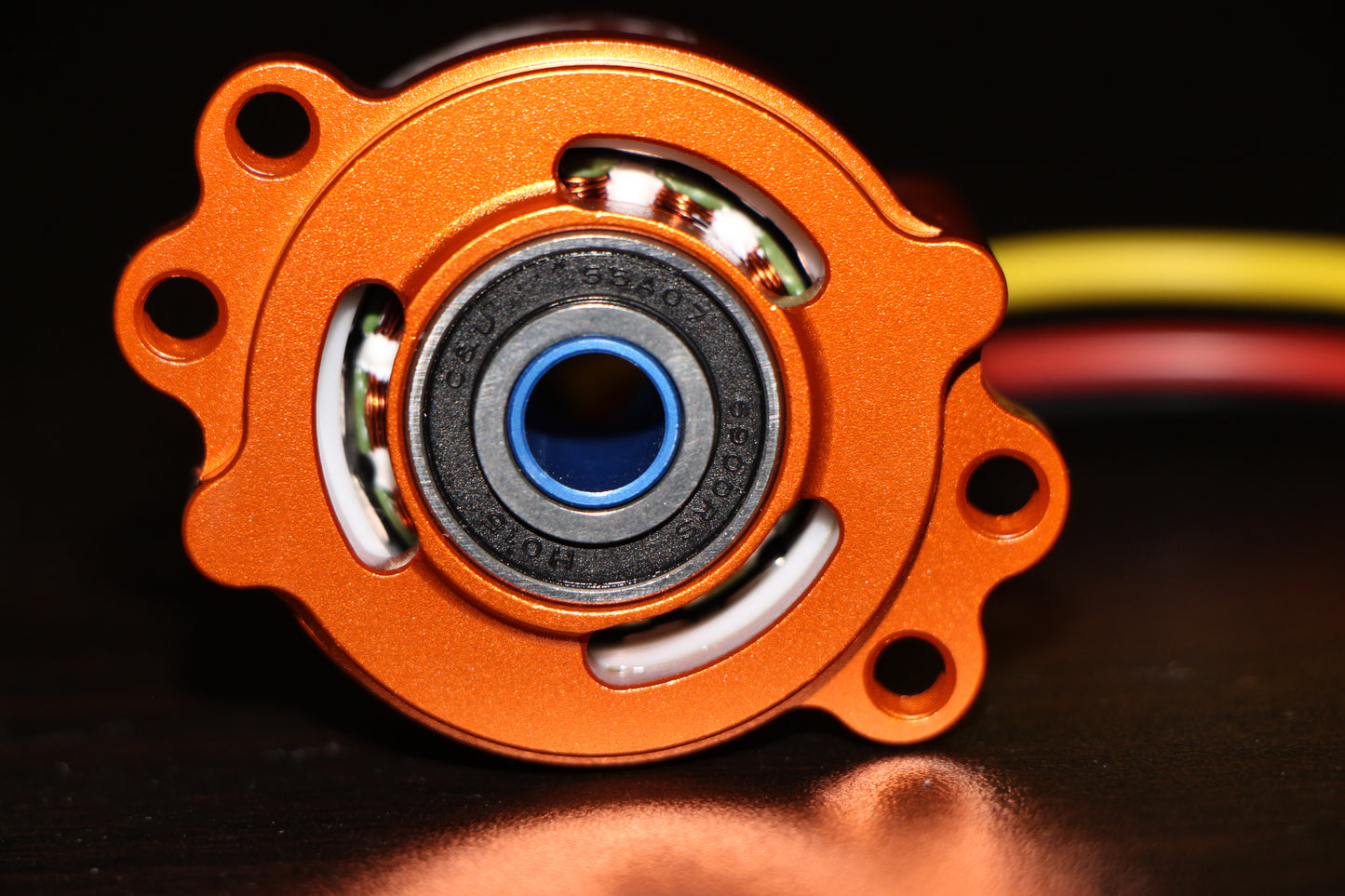
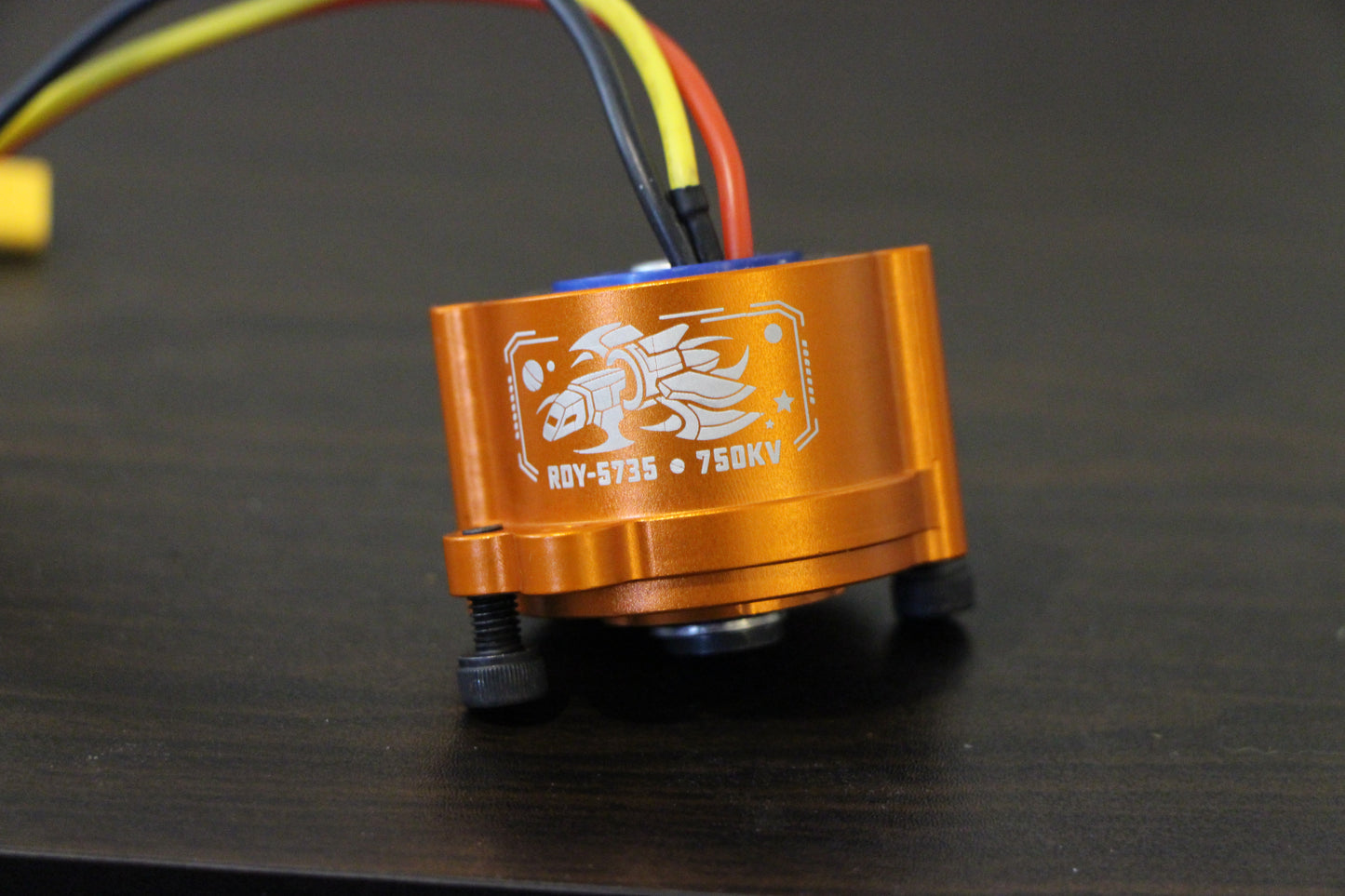
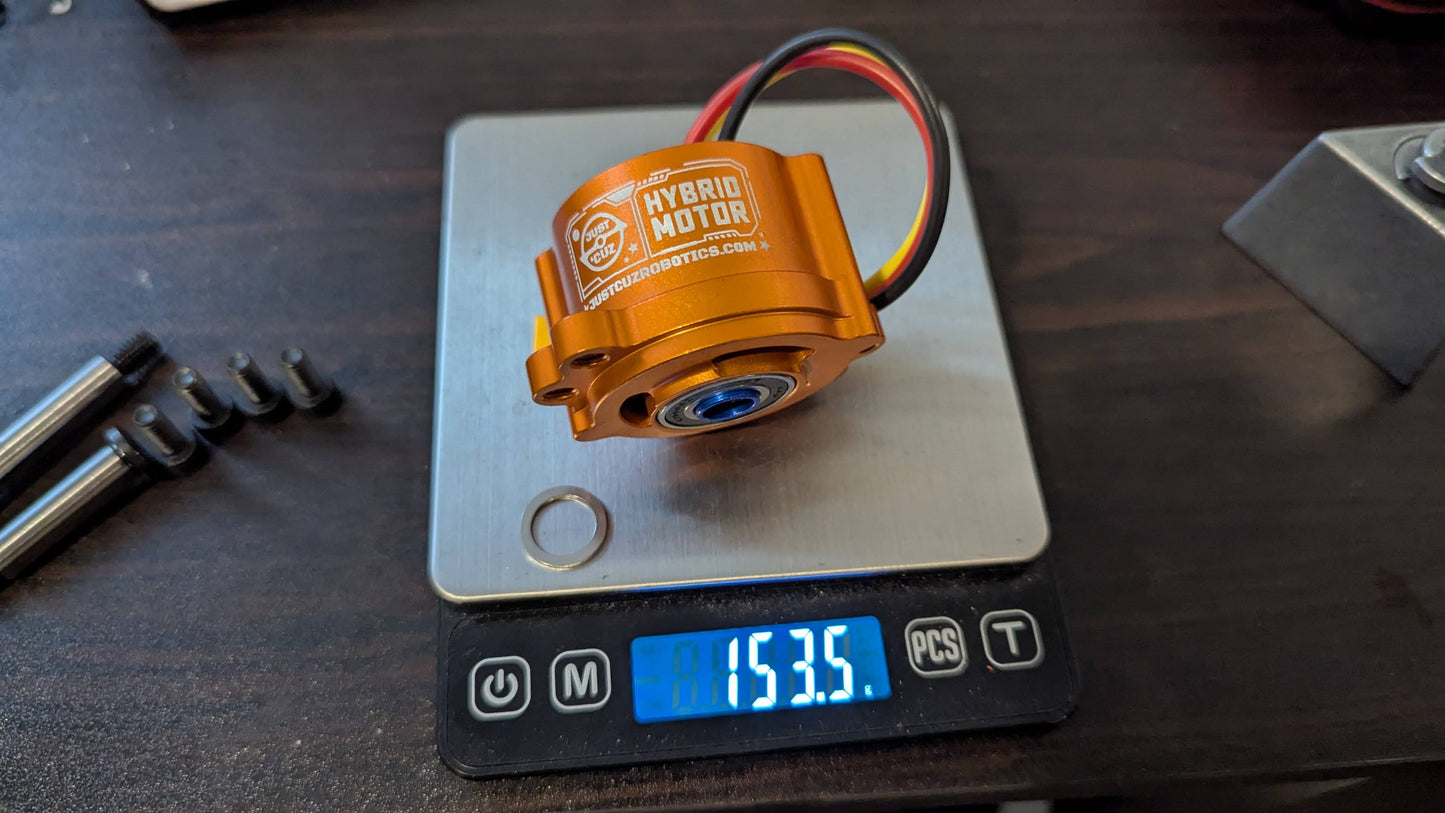
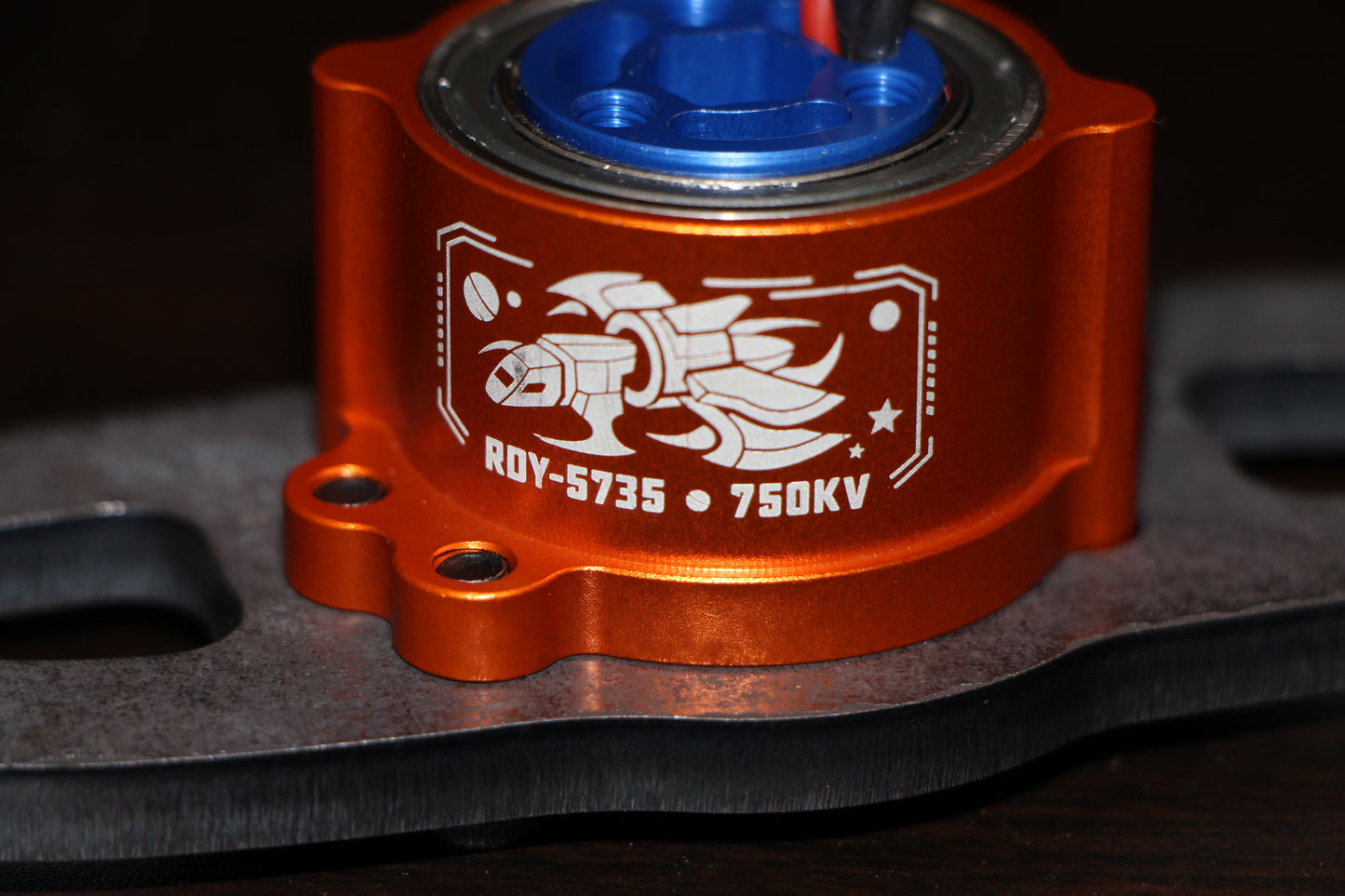
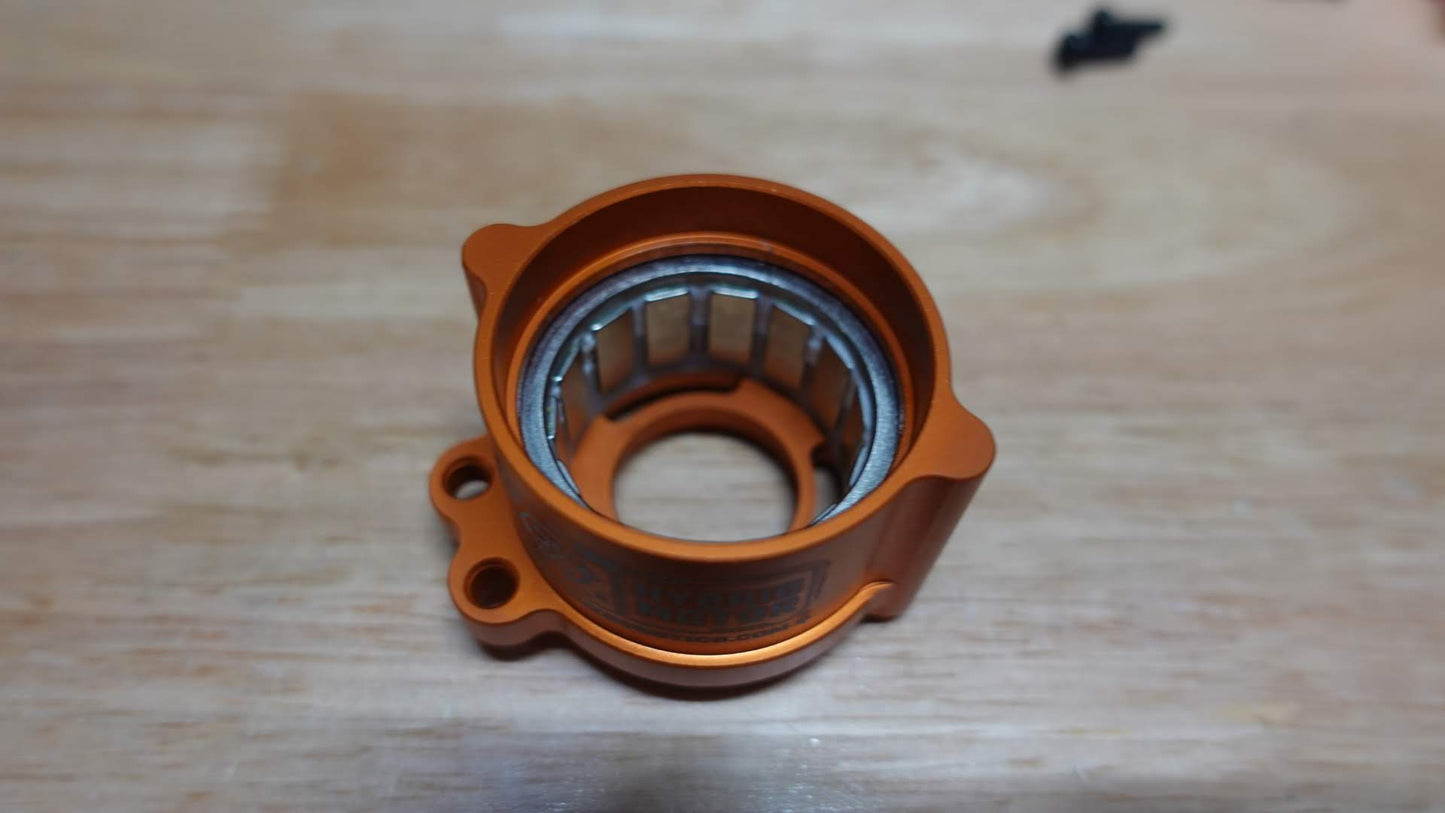